The Opportunity
adi Automotive was approached by Wipac, a lighting supplier to high end OEM vehicle manufacturers, to tender for the design, manufacture and commissioning of the manual and automatic assembly stations required for the rear and side lighting to be fitted to a new model electric vehicle being manufactured in Germany.
The OEM required LH & RH rear light units, a central tail light and LH & RH side indicator units, all to be supplied in two variants.
The adi bid was successful on price and delivery, with Wipac feeling confident of support as they moved into a continuous flow production requirement.
The Solution
adi analysed the Takt time demand, designing and configuring each assembly station for a balanced assembly flow which would meet the production requirements. The component location points on each station were configured to recognise model variants, and the necessary Poka-Yoke error prevention designed in for an error free assembly process.
The build process required robotic arm ultrasonic weld operations, with appropriate safety isolation via a light curtain.
The robot weld cells were designed with an initial high resolution camera recognition step to confirm the model variant light spread and intensity prior to the weld operation commencing.
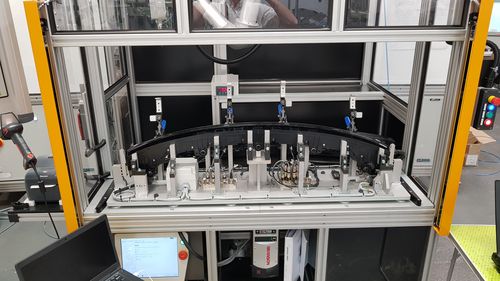
Assembly stations were designed with Desoutter tooling and step by step display screens controlled by part location sensors in the assembly jig.
The final assembly stage was a robot sealing cell for the installation of the clear lens cover. This cell was designed and configured with an internal and filtered positive air flow to minimise any lens contamination.
All assembly stations and cells were designed and configured where necessary for a rapid and accurate change over of the location fixtures for LH or RH units.
The Benefits
Once delivered and and commissioned at Wipac the assembly line operated at the designed cycle times and the lighting units produced were at the required quality level. This was witnessed and signed off by the NPI team from the OEM.
Engineers at Wipac worked with the adi commissioning team to ensure a smooth project hand over.
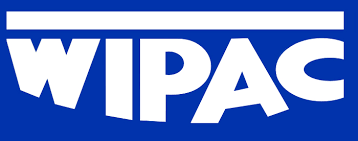
Supplier of vehicle lighting units to 'high end' OEM automotive companies.
Single point of contact project management
Robot cells
Ultrasonic welding
Multipurpose fixtures